Rechargeable Batteries
Industries » Rechargeable Batteries
- BATTERY PACK SOLUTIONS
Fralock supports rapid growth in the energy storage sector by providing battery pack manufacturers with high-reliability component solutions. Battery manufacturers face a multitude of challenges, including design and production of batteries that optimize power, energy density and charging time, maximize cycle life and application value, while minimizing cost, simplifying manufacturing, and ensuring operational safety.
Why Consider Fralock?
Quality Critical Components
Fralock has built its reputation as a problem solver by leveraging our expertise in material selection and manufacturing, and “designing in quality” from the start. With extensive materials expertise, a variety of manufacturing capabilities, and a robust quality system, Fralock provides critical components to satisfy the most rigorous requirements of your battery module and pack.
- Our expertise in thin, flexible materials enables design improvements including more compact designs for smaller batteries with higher power density.
- Robust sealing solutions provide lasting protection from external elements, promoting longer battery life.
- Simplifying assembly, decreasing recycling costs – we design application aids that reduce assembly time, increase placement accuracy, reduce costs, and increase throughput. By using alternative materials, we can simplify disassembly time and costs.
- Our broad range of materials gives you greater flexibility in design and manufacturing in a one-stop-shop, with specialty engineered materials (foams, rubbers, elastomers, silicones, polyimides, laminates, pressure sensitive adhesives), flex circuits and heaters, and ceramics
- Innovative Flexible Circuits – In addition to traditional flex circuit technology, Fralock offers proprietary adhesiveless polyimide lamination for flex circuits that mitigates delamination, accommodates tight radius bends, and extends circuit life in harsh conditions.
THERMAL MANAGEMENT
Thermal Insulation and Thermal Blocking Materials
Thermal management for batteries is an important element of design and operation. When a battery is charged or discharged, it generates heat due to the internal resistance of the cell and the conversion of energy. This heat can cause a range of issues, including reduced battery performance, degradation of the cell’s components, and safety hazards like thermal runaway and fire.
A crucial aspect of preventing thermal propagation and ensuring safety is effective heat blocking and insulation. To manage thermal insulation, prevent thermal runaway, and provide electrical insulation for optimal thermal management and safety at the module and pack levels, we offer a diverse range of passive material solutions.
Thermal Insulation and Thermal Blocking Materials
Thermal Insulation and Thermal Blocking Materials
- PET-based Materials: Known for their excellent thermal stability and electrical insulation properties, PET-based materials are used in various forms such as films and fibers to provide a lightweight and durable insulation solution.
- Mica: This naturally occurring mineral offers exceptional thermal resistance and electrical insulation, making it ideal for high-temperature applications within battery systems.
- Aerogels: These highly porous materials are known for their low thermal conductivity and lightweight nature, making them perfect for thermal insulation in battery packs where space and weight are critical factors.
- Silicone-based Foams and Elastomers: These materials provide excellent thermal insulation and flexibility, which helps in absorbing shocks and vibrations, thereby protecting the battery components.
- Rubbers and Gels: Used for their excellent sealing properties and thermal stability, which help in preventing thermal propagation and maintaining the integrity of the battery pack.
- DuPont TM Cirlex®: A polyimide-based material, Cirlex® offers high thermal stability and electrical insulation, making it suitable for use in demanding battery applications.
- Engineered Technical Ceramics: Ceramics are used for their high thermal resistance and electrical insulation properties, providing protection against thermal runaway and electrical malfunctions.
Thermal Interface Materials
Thermal Interface Materials (TIMs) in battery packs are used to enhance heat transfer between the battery cells and cooling components, ensuring efficient thermal management. These materials help dissipate heat generated during operation, preventing overheating, improving battery performance, and extending the lifespan of the battery by maintaining optimal temperature levels.
Thermal Interface Materials (TIMs) in battery packs are used to enhance heat transfer between the battery cells and cooling components. They help dissipate heat generated during operation, preventing overheating of the battery by maintaining optimal temperature levels.
Fralock’s TIMs include silicone and graphite-based materials, and gap fillers.
Fralock develops novel laminates with integrated systems that go above and beyond a single material to provide a superior solution.
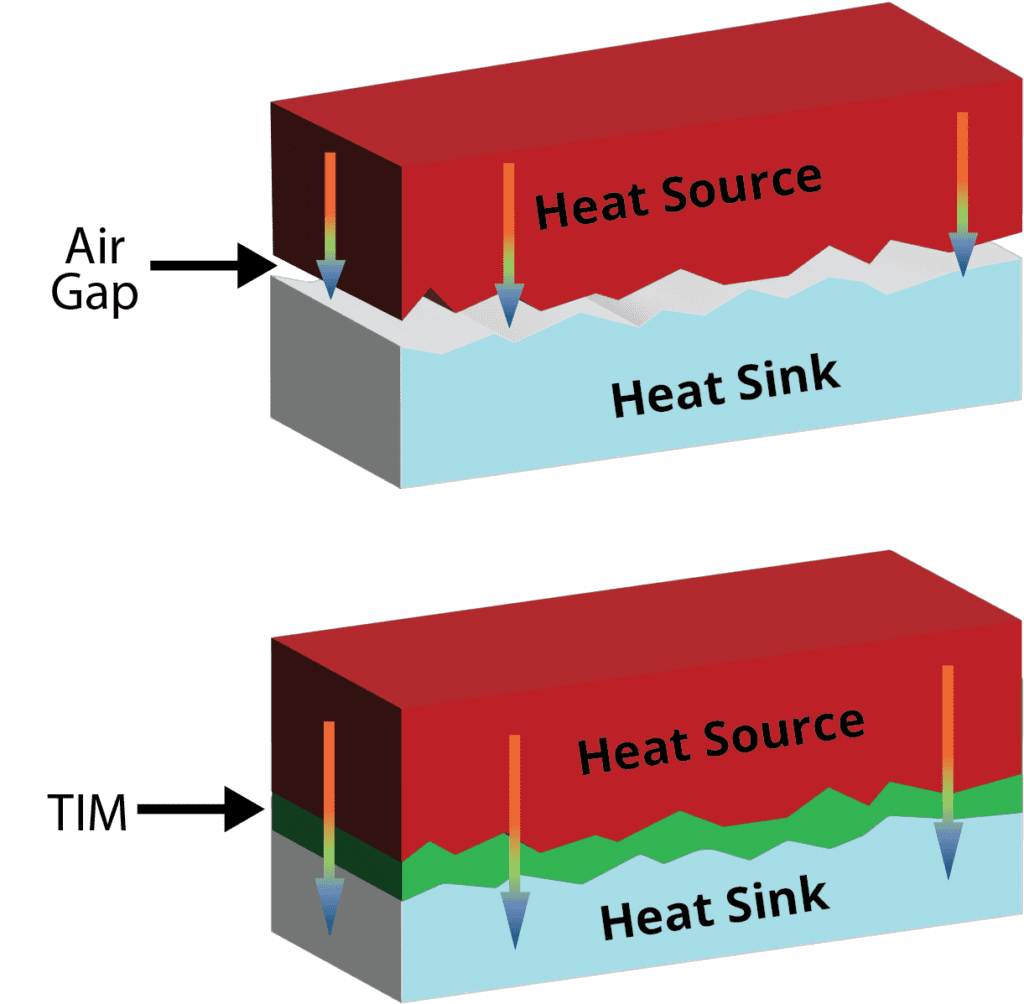
Flame barriers and flame resistance
Battery thermal runaway is a phenomenon in which an increase in temperature within a battery causes a chain reaction that leads to further heating and potentially to a fire or explosion. For thermal runaway prevention, several measures can be taken, including using materials and designs that can block heat, and block or retard flame.
In addition, electrical insulation helps prevent sparking and short circuits, improving battery safety and reliability. Shorting can occur between the anode and cathode, and between the electrodes and the battery casing. To prevent these short circuits, batteries are often designed with materials that are both thermally and electrically insulative.
Fire-protection tapes, foams and films for battery modules and battery packs are used to mitigate thermal runaway.
Fire Resistant/Fire Retardant Materials
Fralock’s fire-resistant and fire-blocking material solutions incorporate a range of products that include encapsulated aerogels, polyimides, and ceramics.
Fire Resistant/Fire Retardant Materials
Fire Resistant/Fire Retardant Materials
- Nomex®
- Fire-retardant polycarbonates
- Fire-retardant polyethylene and polyimides (DuPont™ Kapton®, Cirlex®)
- Avery Dennison Flame Tough™ PET, 3M flame barrier films
- Lexan®
- Kevlar®
- Vespel®
- Fire-retardant polypropylene (Formex™)
- Fire resistant/fire retardant PSA tapes
- Lexan™ films
GASKETS, SEALING SOLUTIONS FOR BATTERIES
- Internal Gaskets, Gap Pads – used for a variety of functions: sealing, insulation, vibration dampening, and compression.
- Environmental Sealing – Typically gaskets that protect from outside dust, dirt, wind, and moisture. Our sealing gaskets can also include EMI/RFI properties.
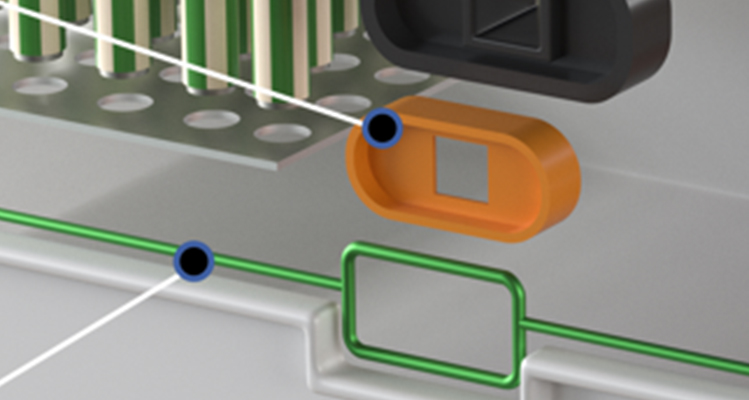

Current Collectors
Current collectors are essential components in batteries that facilitate the transfer of electrons between the electrodes and the external circuit. This component can develop problems such as corrosion, mechanical failure, and overheating. Metals such as copper, aluminum, and nickel can corrode over time due to exposure to the electrolyte or other environmental factors, leading to reduced conductivity and performance.
Fralock sets itself apart with our unique manufacturing and converting capabilities, materials expertise, and ability to hold tight tolerances. This enables us to provide unsurpassed quality workmanship standards that mitigate corrosion and failure, and routinely meet our customers high expectations.
Battery Management Systems (BMS)
Flexible and Rigid-Flex Circuits, Flat Flexible Cables, and Heaters
A Battery Management System (BMS) is an electronic regulator for monitoring and controlling the charging and discharging of rechargeable battery packs, ensuring they operate safely and efficiently. The BMS can be built using flexible electronics that replace rigid PCBs. Flex printed circuits (FPC) are compact and flexible, which makes them ideal for use in applications where space is limited such as a BMS.
There are several applications for flex circuits and flat flexible cables in a BMS system:
- Connect the battery cells to the BMS. In a multi-cell battery system, flexible circuits can be used to connect the cells together in series or parallel configurations, allowing the BMS to monitor the voltage and current of each cell individually.
- Connect the various components of the system to the BMS. For example, a flex circuit may be used to connect the battery cells to the BMS controller, which is responsible for managing the charging and discharging of the battery.
- Connect various BMS components together: temperature sensors, current sensors, and voltage sensors, and cells to the sensors.
- Flexible heaters can be used to heat battery packs in environments of extreme cold temperatures, such as space, and high-altitude and latitude environments.

Why Use Flex Circuits Over Rigid PCB?
- Space and Mass Reduction – In applications where space and weight are restricted, FPC’s and heaters may be optimal. With a low profile and light weight, and FPC can fit into small areas with tight spaces and save in weight compared with a rigid PBC.
- Increased Design flexibility – Flexible circuits and heaters can be designed to follow complex 3D shapes or curves, which can enable new design possibilities and product features that would be difficult to achieve with traditional rigid circuit boards.
- Cost savings – In some cases, the use of flexible circuits can reduce costs by reducing the amount of interconnects and parts needed, saving in material and manufacturing costs, as well as simplifying assembly, installation, and disassembly.
- Fralock offers all-polyimide adhesiveless technology, which provides superior performance and durability in extreme environments. We offer a range of flex circuit and rigid-flex assembly types and sizes from large format flat power cables to compact signal circuits.
Fralock’s flexible polyimide printed circuits provide extremely high reliability for your critical BMS system. More than just a fabricator, we offer innovative solutions to help overcome your engineering problems. Our highly experienced engineering team works closely with you to fulfill the stringent requirements that batteries demand. To insure quality of your product, we offer design, prototyping, testing, production, to complete assembly.
EMI/RFI Shielding
EMI/RFI shielding involves placing conductive materials between the electronics and interfering electromagnetic radiation.
Fralock EMI/RFI materials:
Electrically conductive elastomers, foils, fabrics, tapes, and adhesives wire mesh, mesh/elastomer combinations.
Ruggedization - Vibration Dampening and Sudden Impact
Vibration dampening and sudden impact resistance are important considerations for design in batteries used in applications that are subjected to mechanical stresses, such as vehicles, power tools, or portable electronics. In conjunction with proper battery securement, using materials with high shock absorption and impact resistance is highly effective for minimizing these issues.
Fralock Provides solutions using Foams and Rubbers:
Silicone, polyurethane, polyolefins, Rogers Poron® (urethane foam), Rogers Bisco® (silicone foam), specialty laminates, Viton™ , Neoprene, NBR (natural Buna rubber), EPDM, 3M™ VHB™ (very high bond adhesives), fluorosilicone foams and solids


Precision Die-Cut Manufacturing
We offer extensive capabilities and engineering experience in die-cutting for a wide array of shapes and sizes to fit your requirements. We leverage five decades of high-precision fabricating of advanced materials to satisfy your needs. Our customers rely on us to provide, high-performance, reliable parts.
Fralock produces custom parts including pouch cell enclosures, TIMs, EMI/RFI shielding parts, gaskets, seals, labels, and other thin film battery applications.
Fralock’s Battery Components Work in a Range of Applications
- Battery Electric Vehicles (BEVs) – powering propulsion for specialized industrial vehicles, marine-based vehicles, aircraft.
- UPS Systems – backup power for critical applications such as medical equipment and lighting, utilities stations, telecom battery backup systems.
- Medical equipment – powering:
- Small wearables, insertable and implantable active devices including, heart monitors, insulin pumps.
- Mobile equipment including EMCO machines, ventilators, and monitoring devices.
- Military War Fighter equipment – powering radios, headsets, telecom safety base stations, phones, walkie talkies, respiratory communication systems, thermal imaging cameras.
- Satellites and Spacecraft
- Power Tools – Industrial batteries for heavy use tool such as table and circular saws, routers, drills, drill drivers, impact drivers, grinders, nail guns, rammers, and vacuums.
View/Download Literature
Ask us about your next project!
